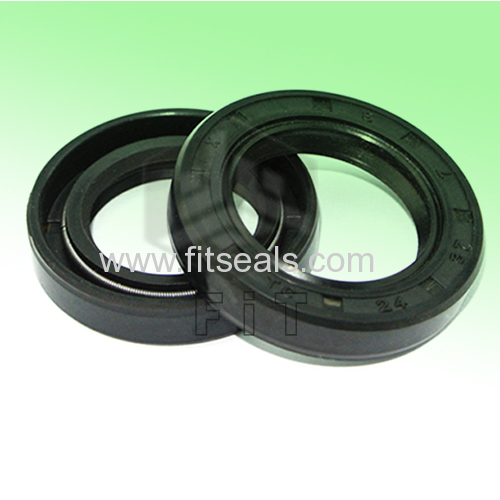
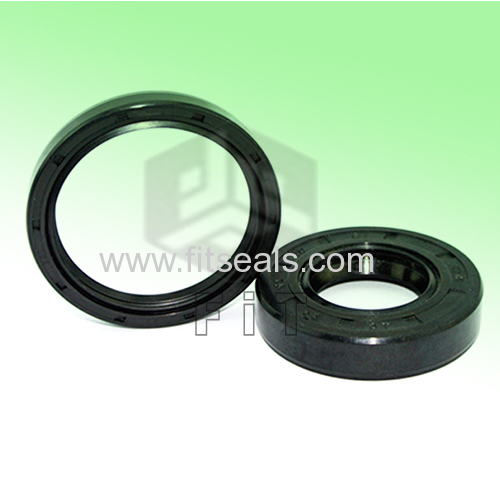

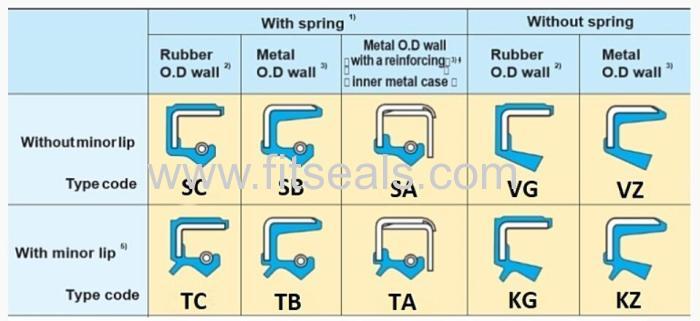
We
offer quality sealing and cost-effective oil seal designs that help
keep equipment running longer while reducing downtime. Through our
comprehensive selection we provide oil seals with short lead times and
with a variety of designs for use in many common and more challenging
industry applications. When selecting an oil seal, it is important to
know what sort of design is needed, and we have outlined a few of the
more common
elements below.
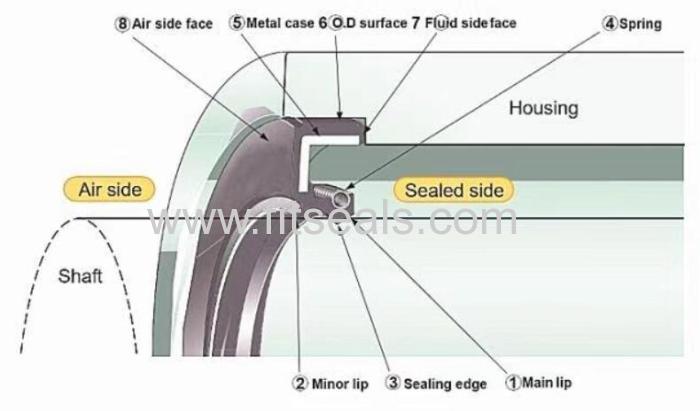
Standard Sealing LIP Designs
oilseals-102-2Our
oil seals have many different available lip designs, with some being
simple and others complex, due to their special application. However,
the most common industry lip standards are described below:
(single
lip): This design uses a garter spring and generally seals against
internal media in lower pressure applications. The single lip is not
recommended for use in applications in which the environment contains
dirt or contaminants.
(double lip): This design is also used with a
garter spring and consists of a primary lip for sealing against internal
media in lower pressure applications. The secondary (also known as the
auxiliary lip) provides additional protection from dust and dirt.
(dual
or twin lip): This design consists of garter springs and two identical
primary lips that are usually used to separate two liquids. The space
in between these two excellent lips must be lubricated with grease or
something similar.
(single lip): This design has NO spring and is
generally used for sealing a non-pressure medium, such as grease or
protecting against dirt.
(double lip): This design has NO spring and
is generally used for sealing a non-pressure medium, such as grease and
is used to protect against dirt as well as internal and external media.
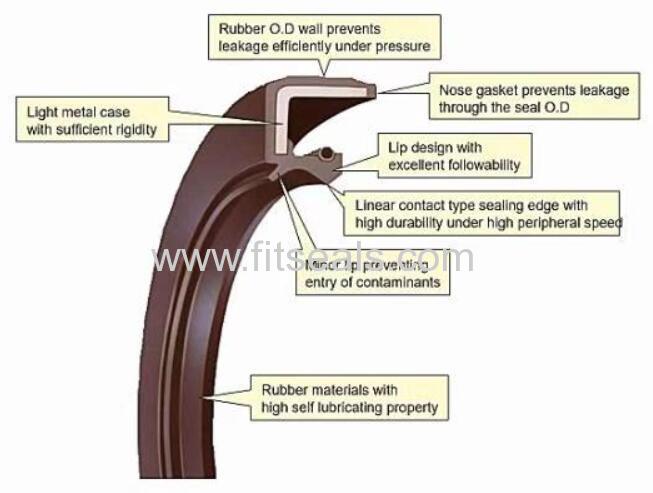
Metal Case Finishes & Treatments
Oil
seals with outer metal cases may include finishes or treatments that
are appliedto the outer edge to aid in rust protection, identification,
and sealing of scratches Or imperfections in the housing bore. Common
finishes applied to the outside edge of metal O.D. oil seals include:
Plain (a bonding agent that is usually a yellowish-green color), a Color
Painted edge, and a grinded-polished edge.
Oil Seal Style Selection (Common Types)
Combining both the lip and case types explained above, it is easy to assemble the Global
O-Ring and Seal (GOR) types as indicated in the following examples:
Type SC: Single lip w/spring, rubber covered O.D.
Type TC: Double lip w/spring, rubber covered O.D.
Type SB: Single lip with spring, metal O.D.
Type TB: Double lip with spring, metal O.D.
Type SA: Single lip w/spring, reinforced metal O.D.
Type TA: Double lip w/spring, reinforced metal O.D.
Factors in Oil Seal Selection
Our oil seals are available in both inch and metric sizes and are selected as follows:
Type: Combination of lip design and case type.
Shaft
Diameter: The outside diameter of the shaft where the seal will operate
(sometimes referred to as the I.D. of the oil seal)
Bore Diameter:
The inside diameter of the bore housing where the seal will operate
(sometimes referred to as the O.D. of the oil seal)
Width (or Depth): The depth of the bore (also known as the width or height of the seal).
Note:
When the width of the seal is not strictly specified, the depth of the
bore is usually made big enough so a seal might be replaced by a wider
one.
Sealing Lip material
Any special materials or considerations, such as stainless steel for the case and/or spring
Any special treatment or finish such as painted, polished edge, etc.
Oil Seal Designs From Global O-Ring and Seal
Global O-Ring and Seal offers a full line of oil seal designs in all industry standard sizes.
If you are a distributor or purchaser who may have need for our oil seal products, contact us
today to speak with one of our technical sales associates, request a no-obligation quote, or
place an order online from our extensive inventory.
Advantage
● The structure is simple and easy to manufacture.
● Lightweight and low consumables.
● The oil seal has a small axial dimension, is easy to machine, and makes the machine compact.
● The sealing machine has good performance and long service life.
● The oil seal has certain adaptability to the vibration of the machine and the eccentricity of the spindle.
● Easy to disassemble and easy to test.
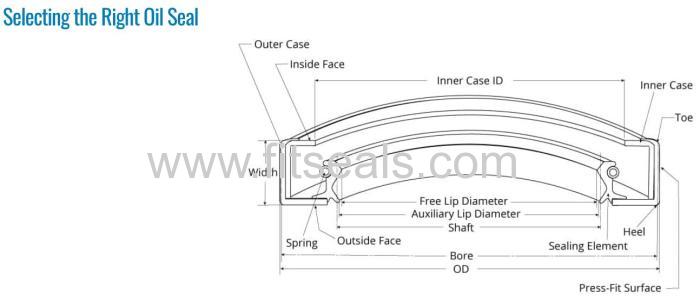
Above,
are all the components of an oil seal and all its naming conventions.
Beyond selecting the correct size, the three primary selection criteria
are Material, Lip, and Case. If you have an oil seal you'd like custom
designed and made, send us your specifications through our Oil Seal
Design Form.
Material Selection:
Material selection is
important to the life of a radial shaft seal. The elastomer's resistance
to temperature, abrasion, chemicals, weather, sunlight, and ozone can
affect a profile's longevity and performance. The two most prevalent
materials are Nitrile and Viton. See our Oil Seal Materials page for
details on compounds and chemical compatibility.
The durometer of
an oil seal is typically dependent on the material it is made with.
Common oil seal materials along with their durometers are as follows:
Nitrile (NBR) Oil Seal: 70 durometer (+/- 5)
Viton (FKM) Oil Seal: 75 durometer (+/- 5)
Polyacrylate (PA) Oil Seal: 75 durometer (+/- 5)
Silicone Oil Seal: 80 durometer (+/- 5)
Lip Selection:
Lip
selection is driven by the media type, shaft speed, pressure,
temperature and contamination parameters. The media used in the majority
of applications is either oil or grease. Lip designs generally include a
spring when the media is oil because of its higher viscosity as
compared to grease. There is also a double spring design when there is
media on both sides of the oil seal. Lip designs can also include a
secondary lip which purpose is to mitigate particulates from reaching
the sealing lip. For additional protection of the oil seal from outside
particulates, a V-Ring can be used in conjunction with the oil seal to
eliminate particulates.
Case Selection:
The most
common and cost effective case materials are stamped from cold rolled
carbon steel. The steel is then phosphate coated to aid in the molding
process and to help eliminate corrosion during storage. A simply 'L'
shaped geometry is the most cost effective case design but a number of
case geometries are available to improve rigidity, positioning and
removability. oil seal cases can also include rubber molded options
which address such factors as corrosion, vibration and sealing
characteristics.